I completed my M.S. in Mechanical and Aerospace Engineering from Oklahoma State University in May 2020. Most of the master’s thesis was completed in my final semester, and this page features discussion of the overall project.
The foundation of this work came from the water-cooled rocket nozzles we studied in Spring 2019 and presented at AIAA SciTech in January 2020. This project was part of our graduate rocket propulsion course, and the most valuable takeaway was a developed understanding of potassium nitrate-sorbitol solid propellant and design of custom research motors.
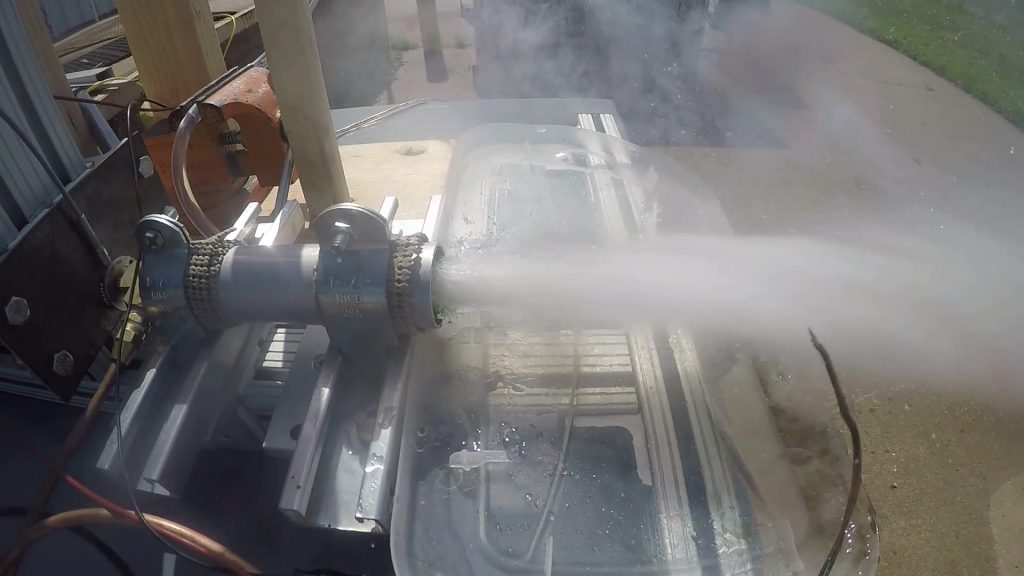
My thesis sought to go into greater detail for quantifying the influence that a water cooling flow had on extracting heat from a rocket nozzle during the propellant burn. In the previous class project we only had access to polymer 3D-printed nozzles that couldn’t withstand the combustion gas temperatures, even with a cooling flow. Fortunately for my thesis, I was able to get help from on-campus 3D printing resources and get several parts printed of stainless steel for my nozzle tests. The tests specifically examined segmenting the cooling passage into multiple smaller channels, so as to evaluate if greater segmentation led to improved cooling effectiveness.
Because of COVID19 (and me waiting until the final semester to really kick things into gear), there was some delay in getting my nozzle printed, but 2 weeks before my defense, I had them in hand and could run my tests. I also developed an analytical heat transfer model at this time to attempt to validate my experimental findings.
Ultimately, while the nozzles withstood repeated hotfire tests, small gaps between the printed layers (due to the atomic diffusion additive manufacturing technique) allowed enough combustion gas pressure to seep through the wall dividing the exhaust gas nozzle passage from the cooling flow passage, thereby preventing water from flowing through the nozzle for the entire duration of the burn. There weren’t any obvious trends by adding more cooling passages, and the analytical model gave wildly different values for cooling liquid temperature increase. 3D-printing at this scale for rocket propulsion systems is feasible, and it is recommended that further research repeat the experiment with metal nozzles using a powder-based printing technique.
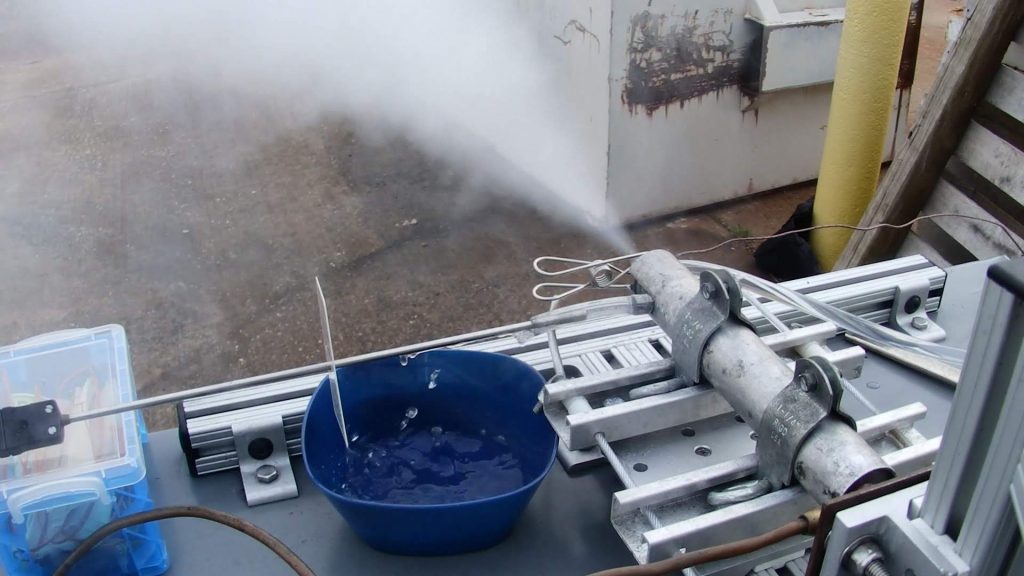
Nonetheless, I passed my defense, and I’m really glad to have worked on a project of such interest to me. Downloads to the thesis document and defense slides can be found below.