Getting Ready for LDRS 38
August 20, 2019
LDRS is coming up next week in Argonia, KS, and I’m thrilled to be attending and bringing several projects to launch. My parents are also coming up to visit for a day, and I’m inviting several of the Mechanical and Aerospace Engineering faculty to attend and see what our program has been up to for the past several years.
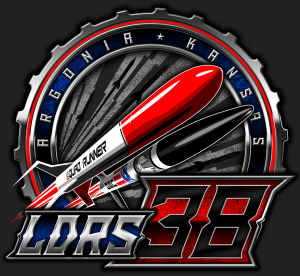
I’m planning to go up as early as Tuesday, August 27th to get a good place to squat for the week close to the flight line and get situated. I’m treating this event as my vacation for the summer. My projects include:
- Odyssey II – CTI L645G to 8500′. My Level 3 project that hasn’t flown since that certification flight in October 2017. I chose this motor for a long 5 second burn trailing a green flame.
- Mach Wave I – research H225, KNSB propellant. My Level 1 and 2 project that, until July, hadn’t flown since the certification flights in fall 2016. Last month on July 20, I did send it up on a research H165, the first launch of a research motor for me! This will be almost an identical motor, but with a smaller nozzle throat.
- Mach Wave II Stage – CTI J760WT to AT I211W multistage. Recently flown earlier this month on August 4th, I’m doubling the impulse in the sustainer to reach 9000′.
- Mach Wave II – AT J350W (sustainer only configuration). Just for funsies and should pull 25Gs at launch.
- TestArticle_FlightConfig_RevIR – AT M1939W. This is one of the Honeywell launchers we flew twice on CTI M3400WTs this summer
In advance of the launch of the H225 research motor, I simultaneously cast a second motor for static testing to confirm good performance (and that it wouldn’t CATO). I fired it off this past Sunday evening which made for a pretty good way to spend my last night of summer!
It is a 38mm, 4-grain motor with a nozzle throat diameter of 0.291″ instead of the 0.345″ diameter throat on previous firings. The motor also featured 1/8″ grain spacers to help facilitate BATES grain ignition and the top grain core brushed with QuickDip pyrogen to quickly ignite all exposed burning surfaces, but I unfortunately still got a hump-shaped thrust curve. It still produced sufficient thrust right from the beginning to safely fly, but I’d really like to get that thrust curve flattened out.
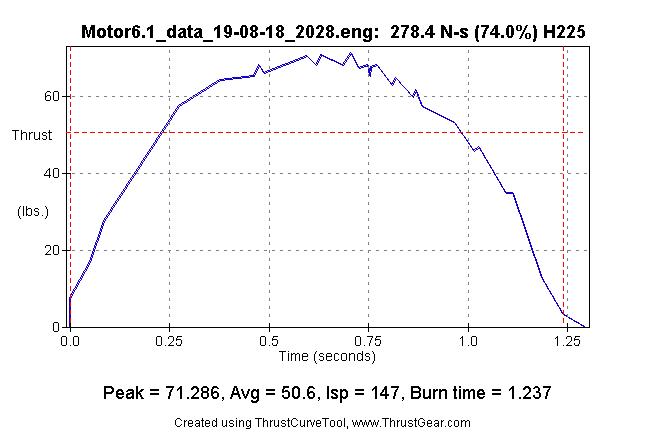
Some other stats on the motor: propellant mass: 0.425 pounds, density ratios 0.931-0.946, grains were within 1.4g of one another, max pressure: 905psi, average pressure: 565psi.
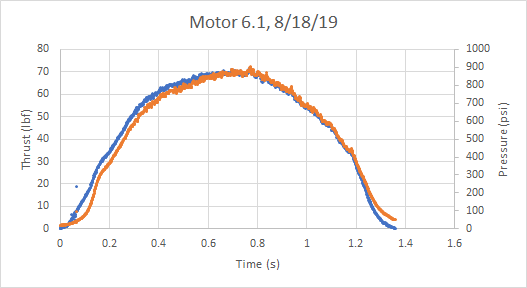
I also made a new rocket room and workshop for myself, something I’ve been wanting to do for years. It is a good workspace for high-power rockets, soldering electronics, and other repairs as necessary. Next time I go home to visit my parents, I’ll bring back the Lego Space Shuttle and Millenium Falcon to add for more decor.
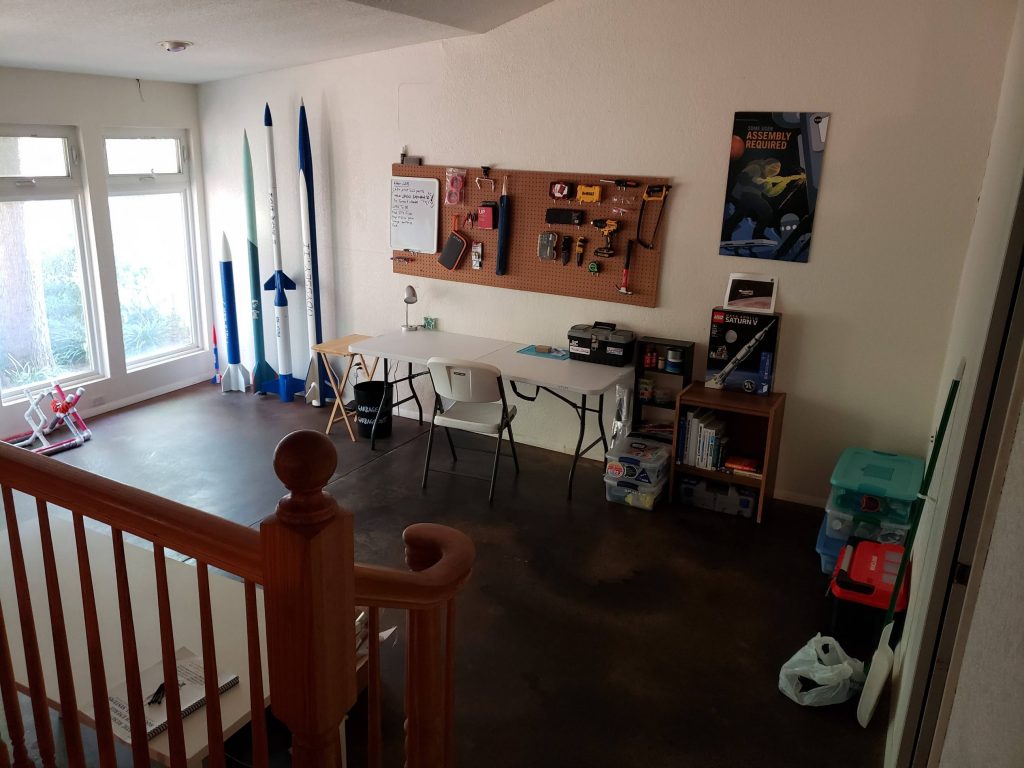
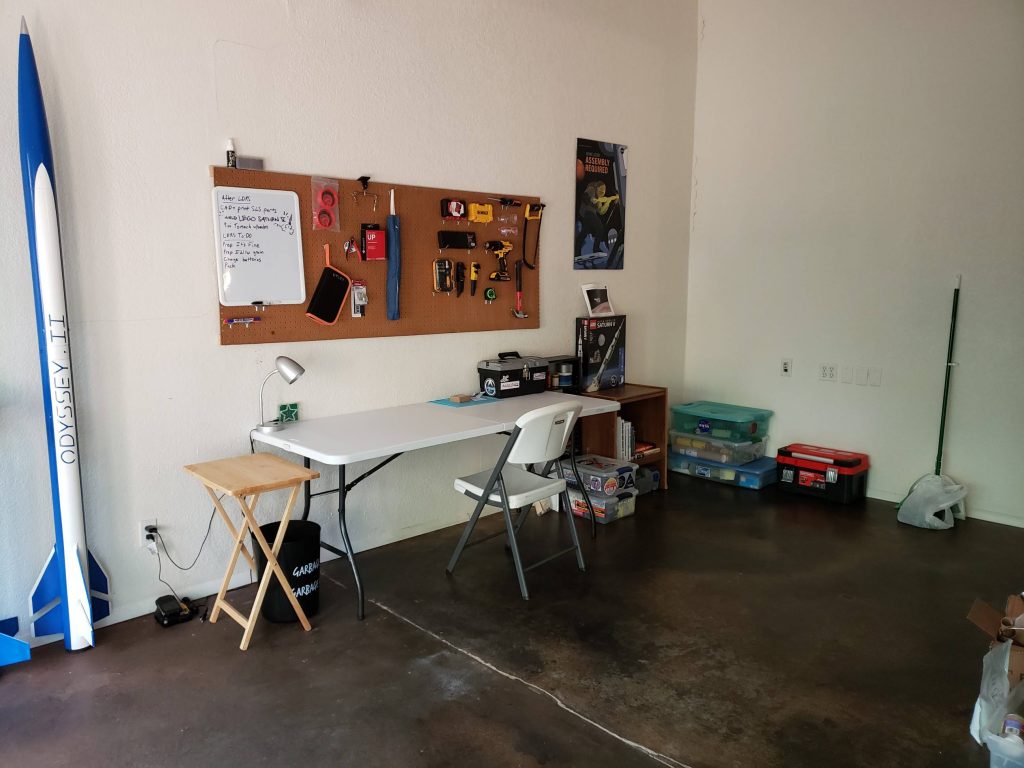